Automate and enhance your productivity with the HALTER LoadAssistant® robotic systems
The LoadAssistant® combines a FANUC robotic arm capable of loading, unloading, sorting, and stacking, with an integrated storage system for a large variety of part types. Keep your production running on 2nd and 3rd shifts, and lights out operation utilizing the LoadAssistant®:
Plug-and-play compatibility with any CNC machine brand
Easy to use HALTER SmartControl with no experience required
Easily moved from machine to machine
Built-in FANUC 6-axis robotic arm with safety area scanner for cage free operation
HALTER SmartControl - Great in easiness to use
HALTER LoadAssistant Models:
Available in various sizes and capacities!
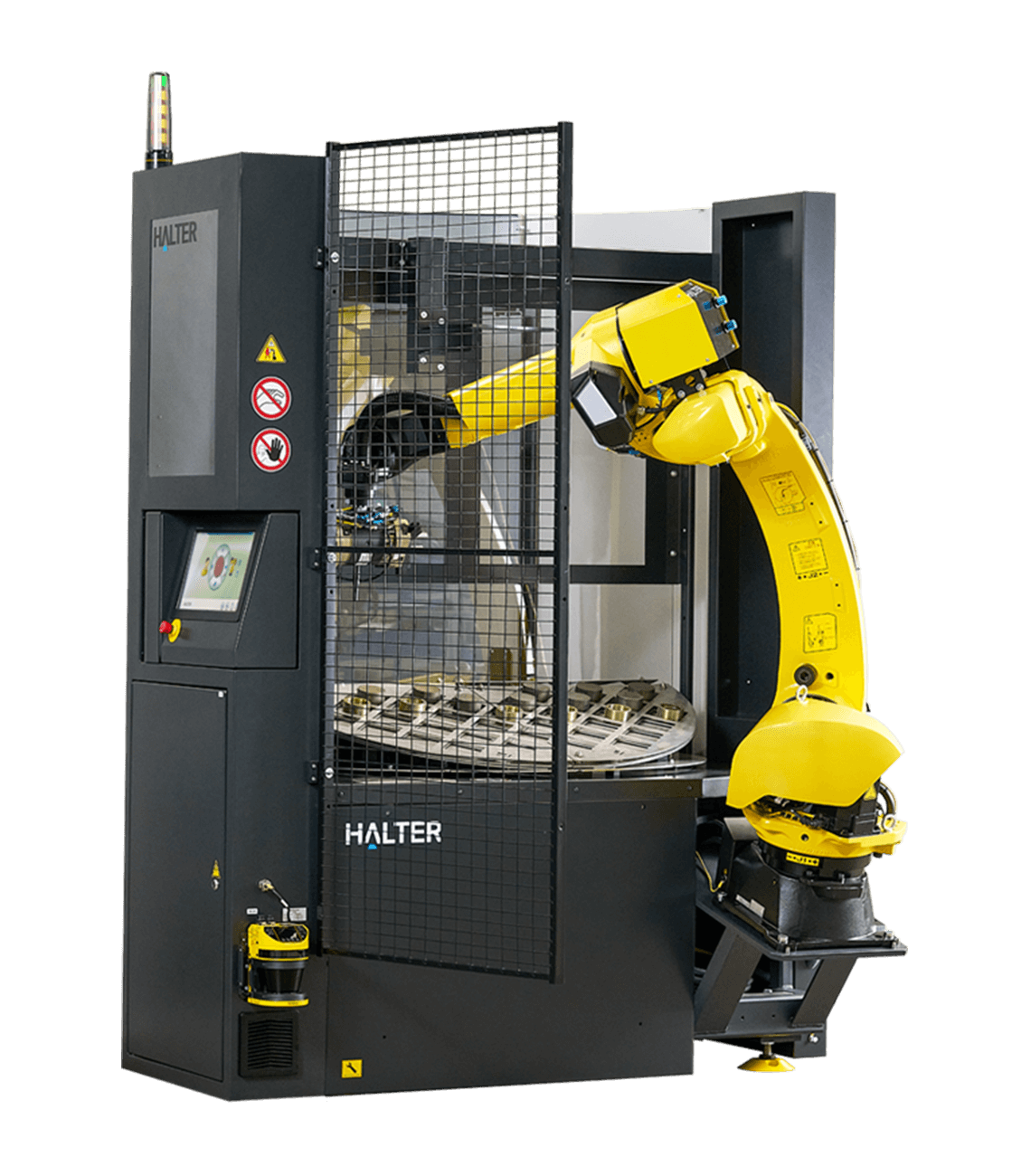
TURNING and MILLING
The Universal stands out as the most versatile on the market, accommodating workpieces up to 300 mm (diameter or LxW) and varied shaft lengths up to 800 mm. Can easily be moved from one machine to another.
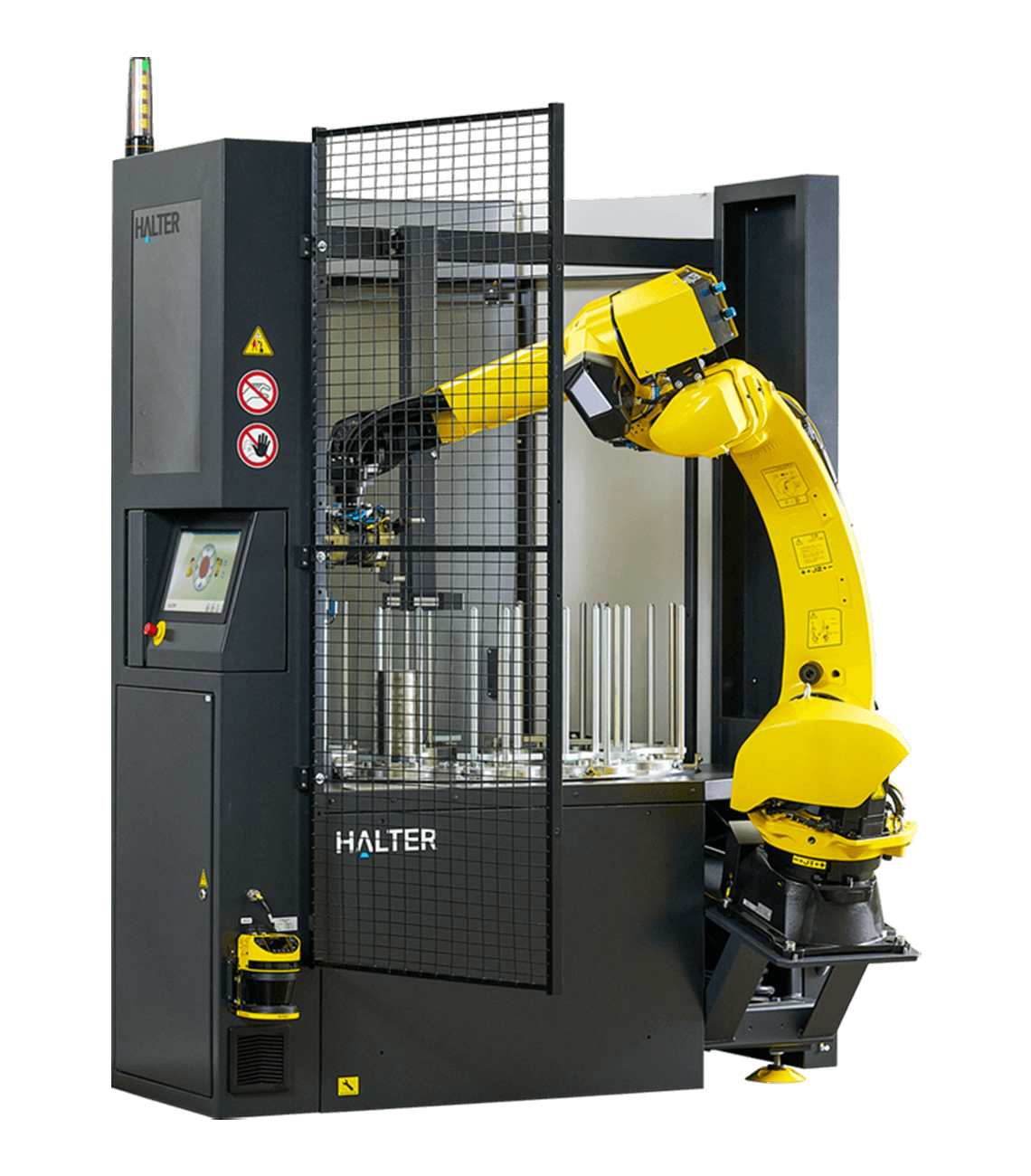
TURNING
The TurnStacker boasts a high capacity for diameters up to 300 mm, ensuring wide-ranging compatibility. Excellent for loading shorter type parts, i.e. flanges, gears, spacers.
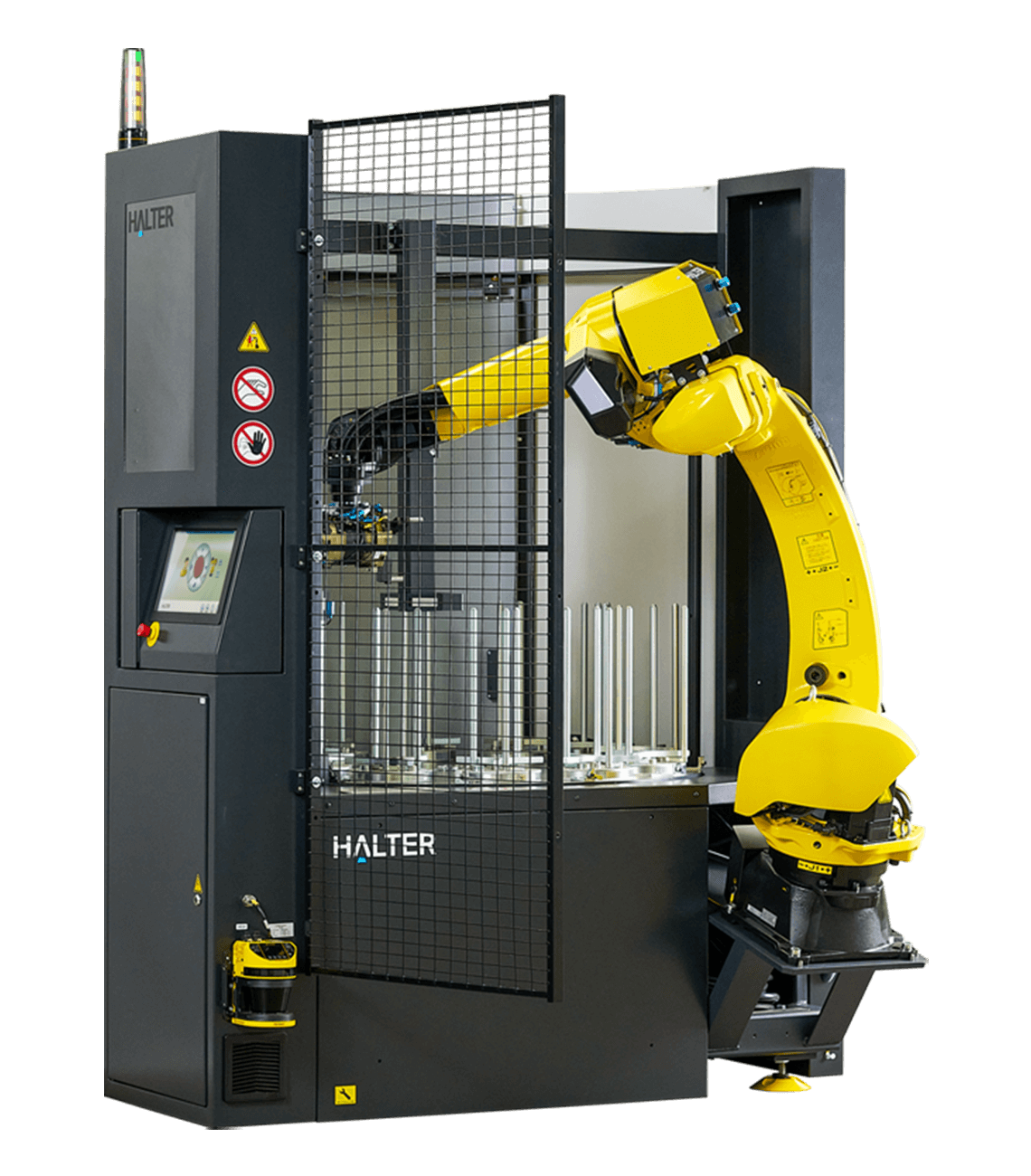
MILLING
The MillStacker offers a high capacity for handling workpieces up to 250 mm Sq. to 100x400 mm Rec. accommodating a broad range of sizes.
Benefits of Halter Automation
Return on investment in 6-18 months
Increased output from more spindle time and reduced idle time
Better turnaround on drop in orders due to quick Halter changeover times
Lights out operation outside of regular working hours with Halter
Decrease hourly production costs
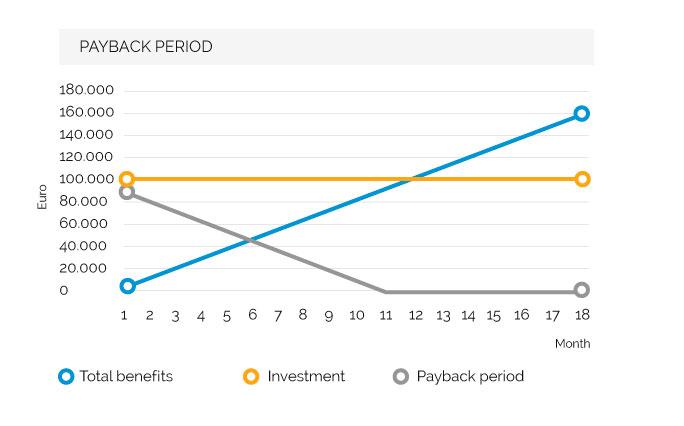
Key Features:

Grid Plate or Stacker System for Maximum Capacity
Universal – pre-programmed grid plates suitable for turning and/or milling parts up to 300 mm. Grid plates are easily adjustable on height and can accommodate parts up to 300 mm tall. Shaft handling option up to 800 mm in length.
MilllStacker - stacking stations designed for higher storage capacity in a compact space with thinner workpieces, up to 250 mm Sq. or 100x400 mm Rec.
TurnStacker – stacking stations designed for high-capacity storage of thinner round workpieces with a diameter up to 300 mm.

HALTER SmartControl
HALTER SmartControl is known for its fast set-up time (less than 5 minutes), and user friendliness. New jobs can be setup and programmed while robot continues operating. SmartControl is completely intuitive; no robotic experience required.
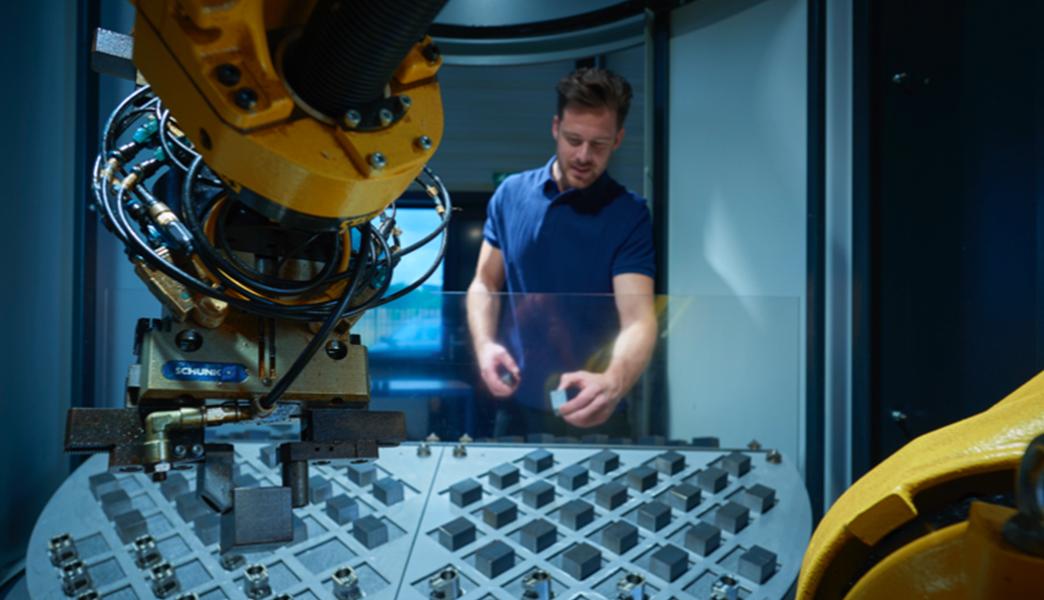
Rotating Loading System Designed for Continuous Operation
New jobs can be prepared, loaded and unloaded, while the robot continues operating. The process does not have to be stopped as the HALTER SmartControl and rotary table can be accessed at all times without stopping the robot process.
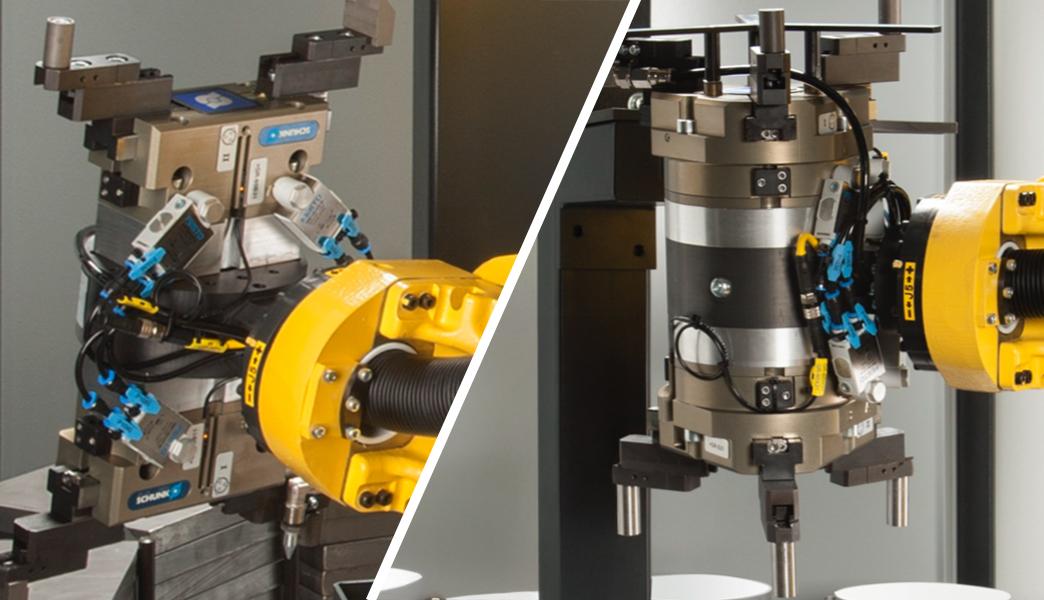
Universal Gripper System
Standard 2-finger gripper package for rectangular parts and 3-finger gripper package for round parts. The quick adjustable gripper fingers are universal and suitable for the complete range of part dimensions as mentioned in the specs of each HALTER model. The built-in grip sensors guarantee a 100% operational safety. All gripper packages are from Schunk.

Highest Quality Industrial Components
Robust construction with highest quality industrial components, plug-and-play system ready for immediate operation. Realizing maximum spindle hours for connected machine.
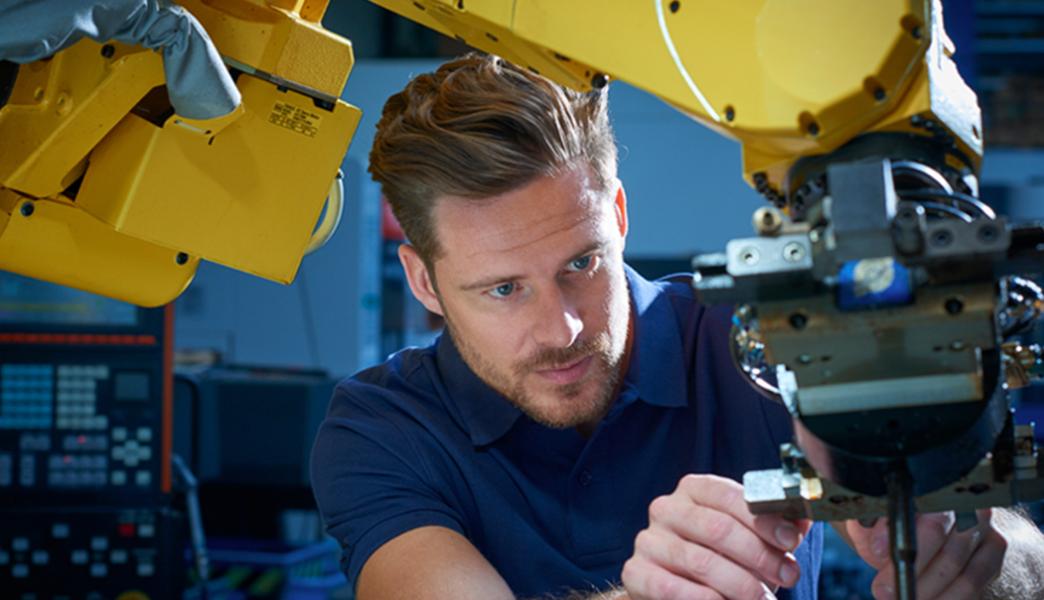
Proven Track Record of 1000+ Installations
With 1000+ installations, Halter engineers have experience interfacing most if not all brands of CNC machines. Complete cell package for easy integration to the CNC machines with or without robot interfaces.
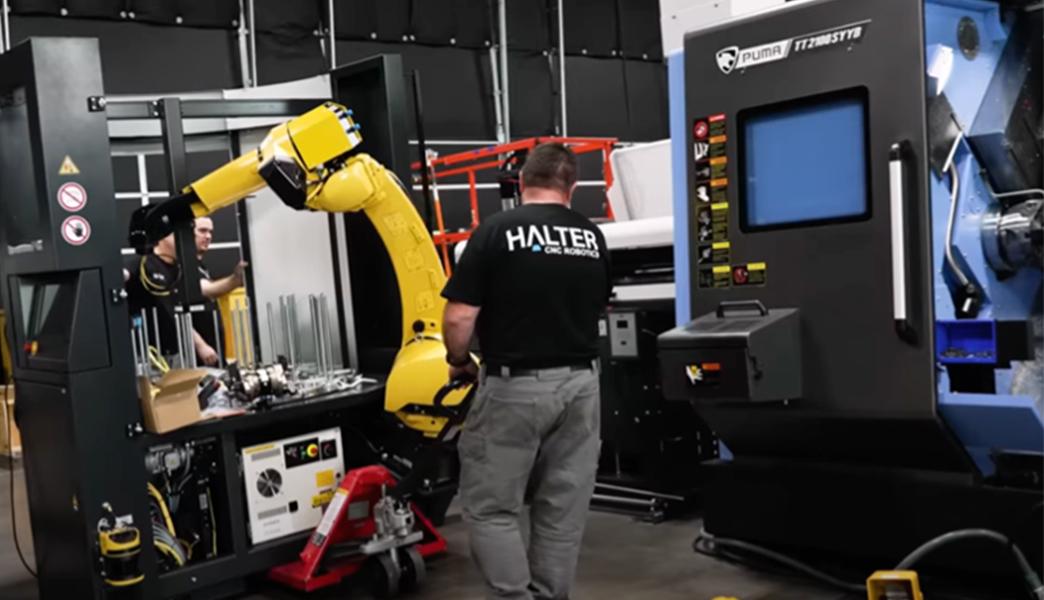
Easy Machine to Machine Portability
Easily move from one machine to another with a pallet jack. The LoadAssistant® utilizes self-centering anchors to increase flexibility between multiple machines.
Key Functionalities:

Loading and unloading of CNC machine
The workpiece is loaded into the CNC machine and after machining unloaded back on the table.

Unloading workpiece on the pallet
The finished workpiece is unloaded onto a pallet after processing.

Unloading workpiece to an external location
A workpiece is unloaded to an external location, i.e. conveyor belt, parts accumulator etc.

Unloading of bar drop
Bar dops can be discharged by means of a special cycle and unloaded to a separate location.

Collecting a workpiece from a pickoff tool
The workpiece is collected from a pickoff tool after machining in the CNC machine.

Cleaning of workpiece outside the CNC machine
The robot unloads the CNC machine and then moves the workpiece to an external cleaning station before the workpiece is placed back into the HALTER LoadAssistant.

Positioning workpiece on measuring station
The robot unloads the CNC machine and then moves the workpiece to an external measuring station before the workpiece is placed back into the HALTER LoadAssistant.

Removal of rejected workpiece
The robot places the rejected workpiece after inspection to a specially defined position.

Workpiece perpendicular-gripping
The workpiece is axially taken from the loading table and positioned on a re-gripping station. Then is regripped perpendicular and positioned in the chuck/vice of the CNC machine.

Radial positioning of the workpiece in the chuck
The workpiece is removed radially by the gripper and then placed in the chuck.

Shaft handling
Loading and unloading of long workpieces, with seamless placement in the chuck/vice, creating high que capacity for shafts up to 800mm.

Workpiece turn-over
For two-sided machining of cylindrical workpieces.

Customer-specific functionality
HALTER SmartControl enables additional functionalities upon customers' specific requests. In this way, the customer retains the advantage of short set-up times through the use of standard cycles, but also keeps optimal flexibility when it comes to adding extra functionalities.