
For the last 50 years, Alabama based PGI Steel has successfully delivered heavy-duty components for automation, construction, oil & gas, power, pulp & paper, government, and defense industries. PGI recently earned its ISO 9001:2015 certification and decided it was time to improve their machining equipment and expand their capacity and productivity.
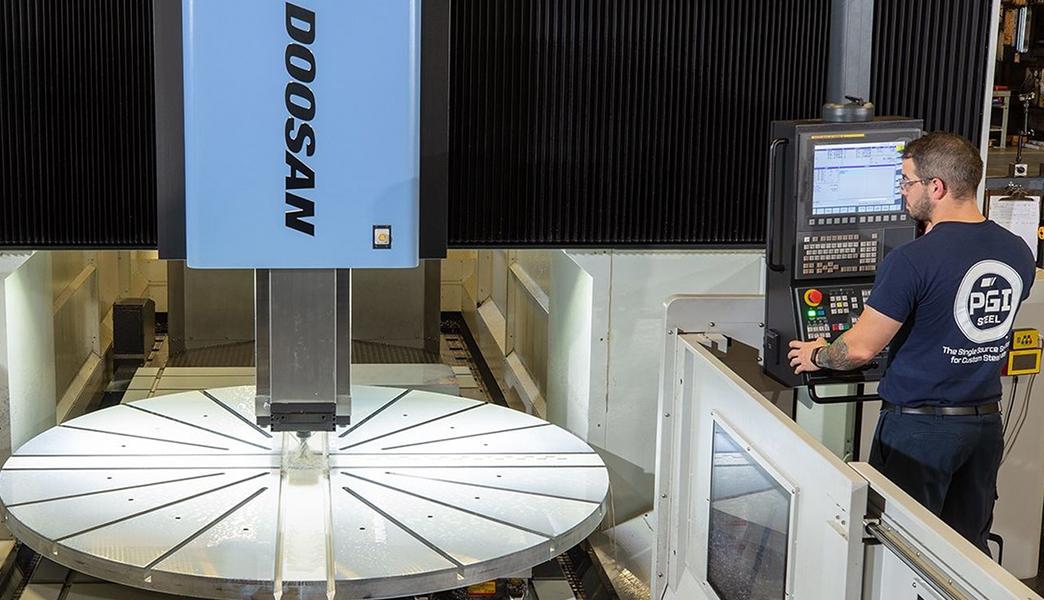
Do it with DN Solutions
PGI Manufacturing Engineering Manager, Rob Russell had previous experience working with Daewoo (now Doosan) machine tools and reunited with Doosan at IMTS in 2018 rediscovering the power and reliability that Doosan Machine Tools had to offer. As a manufacturer of large, high quality, heavy-duty machinery and parts, PGI needed a machine that had the power, quality, and rigidity to match. After consulting with the Doosan and Ellison Technologies team, PGI decided to acquire the Doosan DBM 2540 double column bridge mill. The DBM 2540 features a massive 157.5” x 78.7” table with 39,600 lbs. load capacity, 40 tool magazine, and 8,000 rpm, 73.8 hp spindle with a wide range of optional head attachments like a 90° right angle head.
"Not only did the Doosan perform just as well, it came with more value-added bells and whistles that help with job setups and overall productivity."
The DNM included a 40-tool magazine, oil skimmer, and came standard with Renishaw OMI2 optical receiver and GUI software for the machine to accept a spindle probe and tool setter. To meet high-speed machining and high-quality finish requirements, the DNM 4500S features a 15,000 rpm spindle, 1,653 ipm rapid feed rates, and a Smooth Surface Package for the controls with AICC II 200 block lookahead, jerk control, and nano smoothing.
Full Support from Acquisition to Operation
In addition to a new machine, PGI wanted a reliable support team that offered excellent service and technical support, which the Doosan and Ellison team delivered. Prior to delivery of the DBM, PGI prepared a reinforced foundation for the DBM to ensure optimal rigidity and performance. Although it would take several weeks for the DBM to be delivered, the Ellison and Doosan team were on-site at PGI’s facility well in advance to assist with the installation of the new foundation.
“It really impressed us that they were on-site so early in the process,” he said. “Installation can be a lot to handle with a machine this size, so we appreciated the extra attention.” – Brent Wilson, Marketing Manager, PGI
PGI had expected an eight to ten week installation period, but with the Ellison team’s responsiveness and commitment to their customers, the DBM was cutting metal in six.
“I can’t say enough about the customer service we’ve received from Doosan and Ellison,” Wilson said. “We get quick response on any type of question, no matter what it is. I’m a big fan.” – Brent Wilson, Marketing Manager, PGI
Machining Without Difficulty
From day one, the Doosan DBM 2540 was increasing productivity and producing outstanding results. The DBM reduced 40-hour cycle times down to 11 hours without requiring a lot fine tuning. With the help of their CNC Machinist, Steven Layton, PGI was able to double the recommended speeds and feeds of a 30° 8” face mill thanks to the DBM’s rigid RAM design spindle. The usability of the DBM made programming and machining easy with the Doosan Easy Operator Package.
“The Doosan Easy Operator Package allows you to partner with the machine, quickly fine-tuning the processes.” – Steven Layton, CNC Machinist, PGI
Keeping productivity in mind, the PGI team is determined to get the best cutters and pushing them to their limits to continue increasing efficiency.
Although 2020 has been a rough year for most businesses, PGI was able to find success with their enhanced machining capabilities and contribute to those in need. PGI continued fulfilling orders while finding time to create components for respirator machines and machinery that make N95 masks. Additionally, PGI helped with critical infrastructure for power generation when storms hit Nashville.