
With the growing trend of reshoring supply chain and production back to the U.S., and increasing demands for available capacity and cost competitiveness, manufacturers need to innovate and explore new manufacturing solutions for their shops to be agile and adaptable. These trends have continued to push the development of metal additive manufacturing as a viable solution allowing manufacturers to be more responsive to low volume, high mix production and to create more opportunities in manufacturing complex, seamless parts. Continue reading and view our recorded ChipChat webinar: “Applying Additive Manufacturing to Optimize Your Go-To-Market Timeline,” where our President of Strategic Accounts and technologies, Don McMillan discusses the key elements to consider with additive manufacturing, how the technology works, and how additive fits into your subtractive operation.
If you missed the webinar, continue reading and view the recording.
ChipChat: Applying Additive Manufacturing to Optimize Your Go To Market Timeline
What is Metal Additive Manufacturing?
Metal Additive Manufacturing or 3D printing is a manufacturing process utilizing metal powders and laser technology to create simple and complex seamless parts. With additive manufacturing machines, the powered material is joined or solidified to create or grow parts with the ability to create parts shapes and designs typically unachievable by standard milling and lathe methods. After inputting 3D CAD designs, the machine begins layering powder onto the building platform is then solidified by ytterbium fiber lasers. Once each layer is complete, the table and part are lowered, another layer or powder is added, and the lasers begin solidifying the next layer of the part until completion. Additive manufacturing can create parts in stainless steel, aluminum, nickel, and titanium-based alloys.
Advantages of Metal Additive Manufacturing
Metal additive manufacturing offers several benefits regarding design, production capacity, speed, and repeatability. By utilizing powder-based material and laser technology, additive manufactured parts have virtually zero design limitations with the ability to reduce assemblies by combining multiple components into a single seamless part. Additive manufacturing excels at low volume, high mix production with the flexibility to manufacture single to multiple parts on a single build plate with the ability to easily switch between manufacturing different parts.
Things to Consider
Additive manufacturing is a great solution for numerous applications, but there are several factors to take into consideration before deciding if it’s the right fit for your shop. Be sure to watch the recording as Don proposes and helps you answer the following questions:
- What industries have adopted metal additive parts?
- What kind of parts are you making?
- What is the value of your part?
- What are the biggest constraints for success with your part?
- How many machines do I need?
- What operations are involved post build?
- What is the downstream net profit gain?
About the Presenter
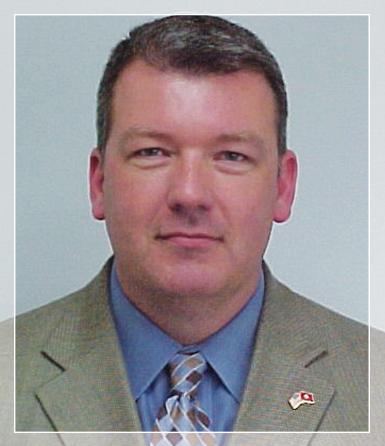
Don McMillan is President of Strategic Accounts and Technologies at Ellison Technologies. He has 35 years of experience using EDM in manufacturing; helping a wide range of customers with process improvements, equipment upgrades and full turn-key engineered solutions. His career history includes: EDM Service Engineer, Applications Engineer and Manager of Applied Technology specific to EDM and 5 axis milling; giving him a full understanding of the challenges manufacturers face on a daily basis. Don is a Certified Tool Maker and a former General Manager of a high volume EDM job shop based in Chicago.
Want to Know More?
For more information or questions about five axis machining, contact cncinfo@ellisontechnologies.com.
View our other recorded ChipChat webinars.