
Are you machining parts with numerous vertical machining centers, the same number of operators, a variety of fixtures, probing cycles, flipping parts, losing time and accuracies, and slim margins? Make the switch to 5-axis and MAKE MORE time, parts, and money. Ellison Technologies’ Product Manager of 5-Axis Technologies, Chris Wood, will walk you through the steps needed to integrate your first 5-axis, understanding machine style selection, and an overview of how your profitability and productivity will be significantly improved. Read along to discover and view the recorded ChipChat webinar, “Expand Into Five – Introducing 5-Axis Technology into Your Business.”
If you missed the webinar, continue reading and view the recording.
ChipChat: Expand Into Five – Introducing 5 axis Technology into your Business
Why Switch to 5-Axis?
As market demands increase requiring higher technology, more efficient processes, and cost saving production, manufacturers can look to 5-axis machining technology. Utilizing 5-axis technology, manufacturers are able to machine more complex parts with higher quality, achieve shorter processes, lead times, and setups, and increase productivity, ROI, and profitability.
Shop and Process Improvements
In most machine shops not utilizing five axis machines, owners may be familiar with machining parts that require multiple machines, setups, and operators, ultimately increasing your labor costs and cycle times. When your spindles aren’t machining while you are doing setups, loading and unloading, checking a part or tool, chip management, inspections, in-process gauging, and operator delays due to multi-machine attending; you’re not making money. By utilizing five axis machines, shops are able to consolidate several machines and setups into one, as well as eliminating processes that normally require edge finders, 1, 2, 3 blocks, tool carts, and sine angle plates.
I Don’t Do 5-Axis Parts
Five axis machines are not just for five axis parts. When you are able to machine on 3 or more sides of a part in a single setup, you’re improving your productivity and profitability. In many situations the average 3-axis vertical machining center can machine simple five-sided parts but may require up to five setups. Complex parts that involve more than five sides may require more than five setups and may need special tooling and vices. In both situations, a 5-axis machine can machine both parts in a single setup, reducing machine attendance time and labor, and giving your operator the flexibility to complete additional tasks.
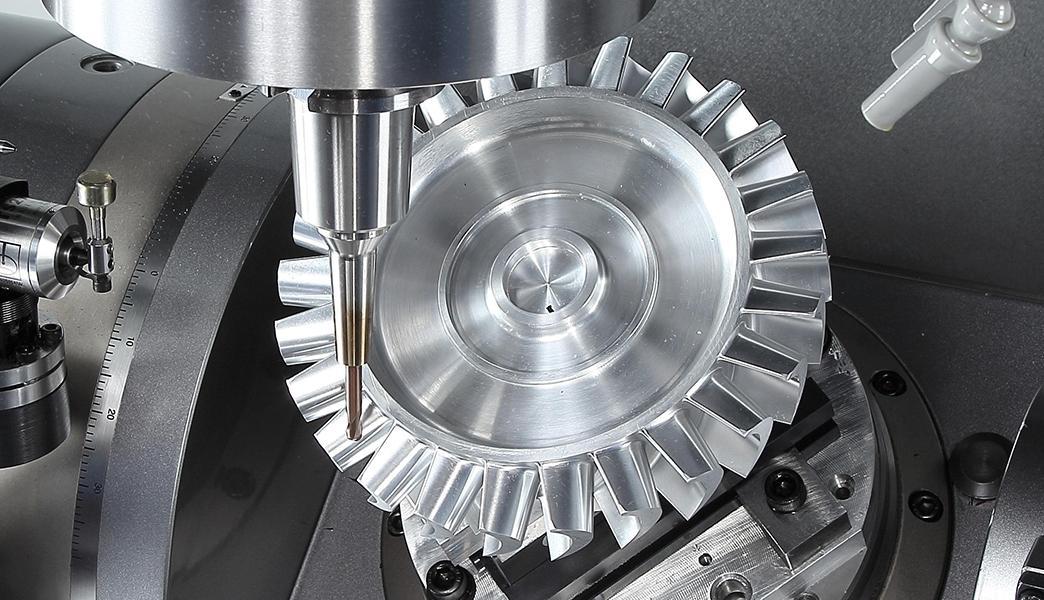
Things to Consider
As you move closer to integrating five axis into your shop, there are several factors to take into consideration to ensure that your productivity is maximized. Deciding on which five axis will be best for your shop begins with the parts you are making. Your checklist for success includes:
- Identifying the parts that would benefit the most from faster setups and unattended operation
- Determining if those parts can be run in one or two operations
- Optimizing the best process for machining those parts
- Understanding your machine spec requirements for those parts
- Calculating your ROI
- Identifying the best CAM solution, post processor, and verification software
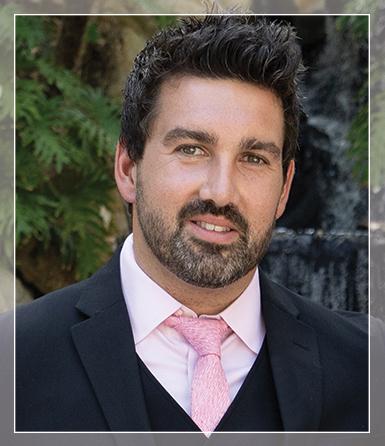
About the Presenter
Chris Wood is the Product Manager of 5-axis Technologies at Ellison Technologies, Inc. Over the past 10 years with Ellison, Chris has helped countless manufacturers transition in to their first 5-axis machine. He is passionate about identifying and helping manufacturers overcome their productivity challenges, and dedicated to helping businesses improve their bottom line through technology solutions and processes.
Want to Know More?
For more information or questions about five axis machining, contact Chris Wood at cwood@ellisontechnologies.com.
View our other recorded ChipChat webinars.