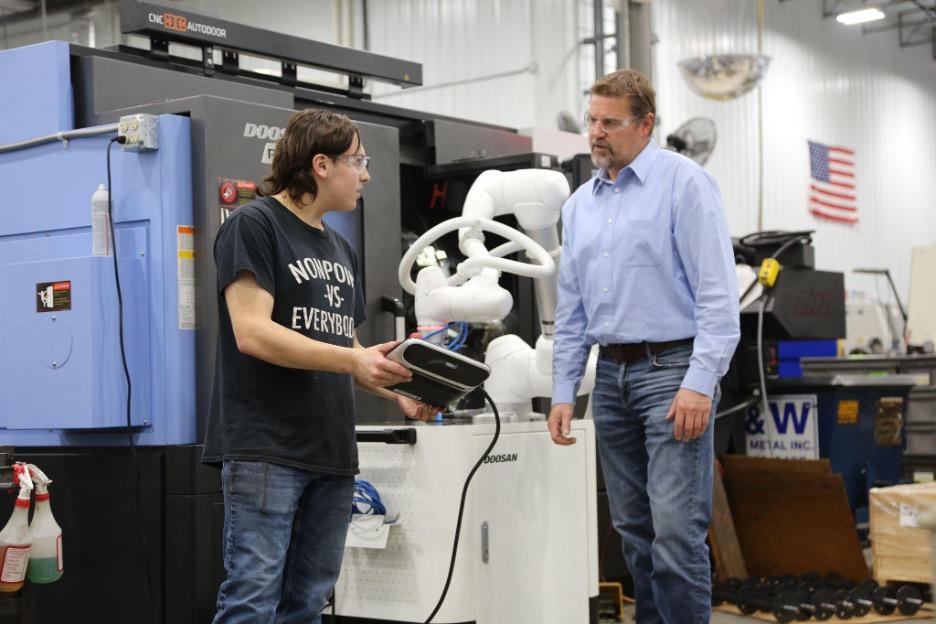
Some shops still have yet to welcome automation, but FZE Manufacturing Solutions is not one of them.
The North Fond Du Lac, Wisconsin shop offers a robust range of machining and manufacturing expertise, and much of the equipment on their floor is automated in some way. All of their multi-axis Swiss machines and several of their turning centers are bar fed and they have a twin-spindle, twin-turret turning center that is equipped with an overhead gantry robot for loading raw parts and unloading finished parts. Additional CNC turning centers are manually loaded and unloaded by Machinists and Operators.
Machining centers feature pallet changers to keep spindles in the cut longer, plus auto doors to remind operators to unload/load parts. And when it came time to add cobots to the mix, FZE reached out to Ellison Technologies
New Challenges
Founded in 1974, FZE has grown to become a full-service supply chain machine shop that manufactures parts for a wide range of industries, including marine, agriculture, firearms, plumbing, hydraulics, safety, special fasteners, and hardware. “We’ve got an absolutely amazing team of people here,” states Doug Pribyl, CEO of FZE Manufacturing Solutions. “Our FZE team keeps a watchful eye on industry trends and technological developments. Next year in 2024 we will celebrate our 50th year since the company’s humble beginnings as a general machine shop and our longevity is due to our dedicated employees and their willingness to adapt to changing times and maintain a cutting-edge competitive approach through it all.”
In 2019, the company received the high honor of being named one of the state's only manufacturers to be approved by, registered, and trademarked with the Made in Wisconsin program. Introduced in 2012 by the Wisconsin Economic Development Corporation (WEDC), this program recognizes the contribution of Wisconsin companies and promotes their good work and skills around the state. “We’re fortunate and proud to be included in this elite group and we use the Made in Wisconsin logo in our promotional materials,” said Pribyl.
Recently, labor challenges have become a bigger issue at FZE. “There is a lot of competition in town for machinists,” said Pribyl. “Hiring is tougher than it's ever been. We’re doing everything we can, including partnering with a local technical college to sustain a CNC boot camp program, as well as training more machinists and operators internally.”
“Each generation has challenges they need to figure out, and automation is a necessary tool to help solve the current difficulties with skilled labor,” said Pribyl. “We look for opportunities to approach challenges from new angles.”
Hiring the Cobots
Pribyl and his team understood the benefit Cobots could bring: they can efficiently handle simple as well as complex tasks, are extremely reliable, and easy to set up. FZE evaluated options from a handful of Cobot manufacturers, and they identified the following technical criteria as must-haves:
- 1 meter reach
- 10 kg (22 lb) payload
- Seamless interface between the Cobot and machine tool. No translator.
- Teach pendant or Laptop connectivity for easy Cobot control, programming and monitoring
FZE did their research and even tested a few options on-site at their North Fond Du Lac facility. After the evaluation process was complete, the Doosan Robotics M-Series Cobots came out on top.
“At the end of the day, we chose the Doosan Cobots because they met our technical needs, and Ellison is already in our shop servicing our Doosan machine tools,” says Pribyl. “We have a fantastic relationship with Ellison on every level, from sales to service to parts to their management team.”
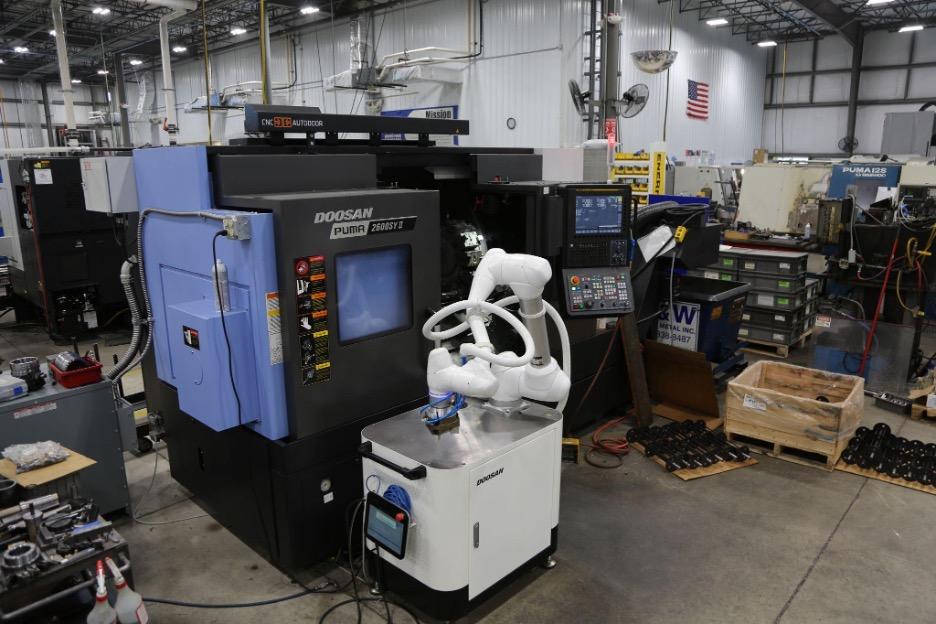
Meet the Cobots
Meet the Cobots
Doosan Robotics M-Series is designed to handle complex tasks with precision and efficiency. Featuring six highly sensitive torque sensors capable of detecting obstructions in the workspace, operators can work safely alongside the Cobot. Additionally, the M-series’ range of models has up to a 15 kg (33 lbs) payload capacity and 1,700 mm (66.9”) reach and is capable of being mounted in a variety of locations including pedestals, walls, ceilings, and floors.
FZE is currently using their two M-Series M1013 Cobots on different applications. The first is on a DN Solutions (formerly Doosan Machine Tools) PUMA 2600SY turning center that is dedicated to chucking applications. The Cobot loads a raw blank into the main spindle, and removes the finished part from the sub spindle.
The second Cobot is partnered with a DN Solutions (formerly Doosan Machine Tools) PUMA TT1800SY turning center with a bar feeder. While many of the jobs on this machine are bar fed in, and then unloaded via the parts conveyor, there are some hydraulic components with super-fine surface finish requirements that could get damaged from traditional conveyor movement. For these applications, the Doosan Cobot removes the part from the sub spindle and carefully places it in a partitioned egg crate container to protect those critical surface finishes.
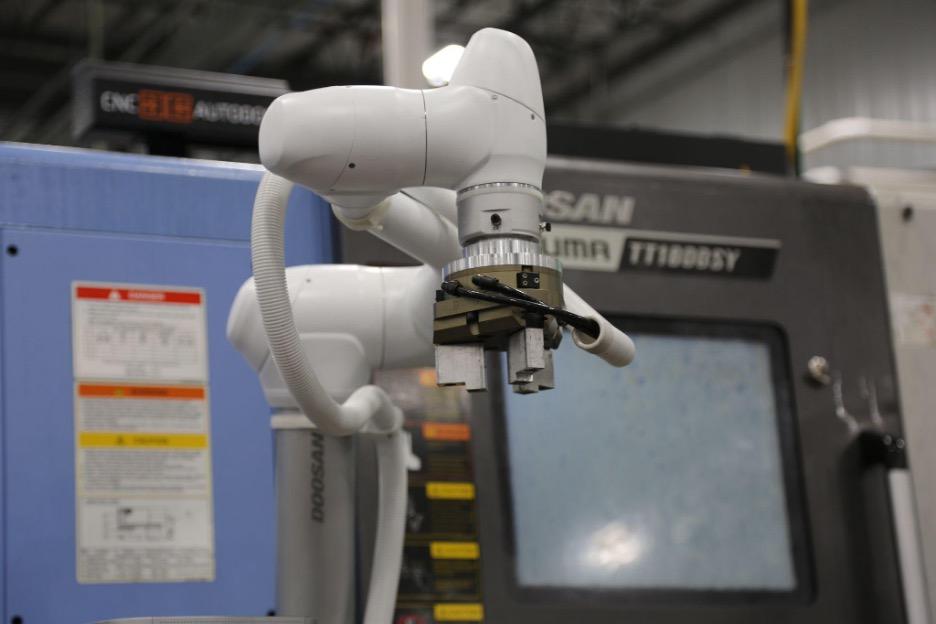
The Ellison Impact
The Ellison Impact
Pribyl (and FZE) has a unique appreciation for the strengths and weaknesses of humans and automation. He admits that while a human can load and unload a part faster than a Cobot, the Cobot always wins the race in the long run.
“It’s a tortoise and hare comparison,” states Pribyl. “Humans can absolutely load and unload parts faster than Cobots, but the Cobots are always there working. They’re consistent and always staying on task, which leads to higher productivity in the end.”
“And although I appreciate automation in our business, I love to deal with real people and passionate trade professionals,” states Pribyl. “Everyone at Ellison has been extremely professional. They take care of our business needs from start to finish.”
If you’re in need of machine tools and Cobots that are just as reliable and productive as the people who support them, talk to Ellison. There’s a dealer in your area, ready to help you get to the next level.