
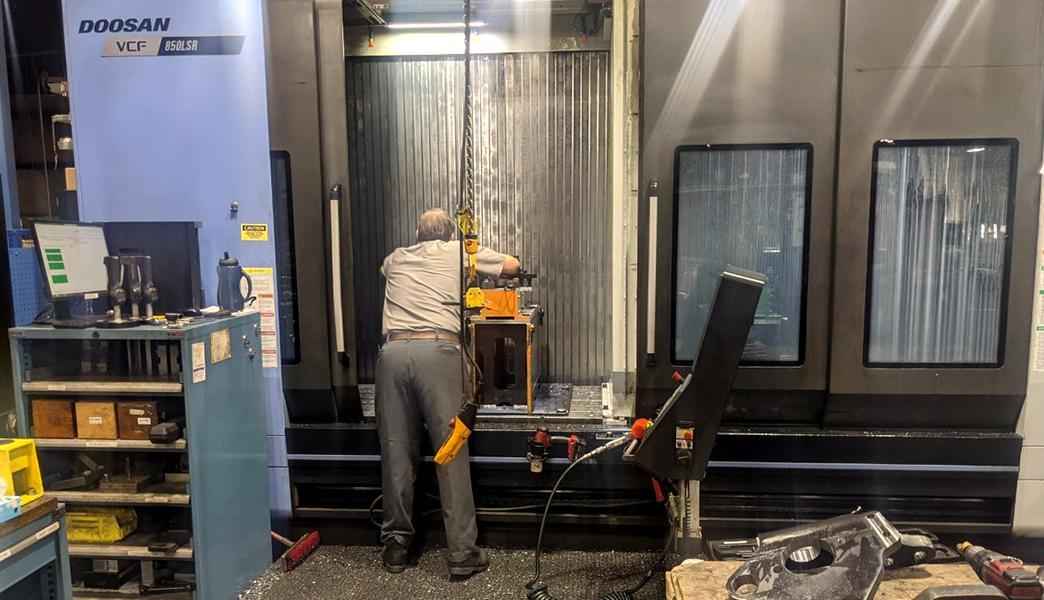
For over four decades, Link® Manufacturing, headquartered in Sioux Center, Iowa, has been committed to developing and manufacturing heavy-duty commercial vehicles and equipment suspension systems. Link’s dedication to manufacturing and delivering quality vehicles and parts has driven their success to achieving a 99.5% On-Time Delivery and OE PPM < 300. Since 2016 Link has acquired five Doosan Machine Tools machining and turning centers including the VCF 850LSR, Lynx 2100LSYB, Lynx 2100LB, and two NHP 5500’s.
With each acquisition Link has continued to increase their productivity and profitability by achieving done-in-one machining, unattended automation, increased spindle utilization, and reduced outsourcing and tooling costs.
The First Doosan
The relationship between Link® Manufacturing, Ellison Technologies, and Doosan began at IMTS 2016. Link’s Manufacturing Engineer overseeing CNC machines, Derek Poppema, worked with Ellison Sales Manager, Tim Petersen, to find an advanced machine to support their evolving business. After discussing options, Derek proposed the VCF 850LSR vertical machining center with HSK-63 taper, 120” wide table, and rotating B-axis spindle to Link’s management team.
"This machine allows the use of a partition on the 140" long table, creating separate work zones. We use this to our advantage, much like a pallet changer, where an operator can be unloading/loading parts while the spindle is machining in the other work zone," Derek said. "Take out the partition and you have the ability to work on very long parts. In our case, that means truck axles."
Through creative fixturing, Link was able to machine multiple parts on the high capacity table, and reduced cycle times on four parts by 50%.
"… we also relocated some casting parts to the VCF and cut cycle times in half," Derek said. "We now run four parts in 30 minutes versus an hour."
Horizontal Productivity
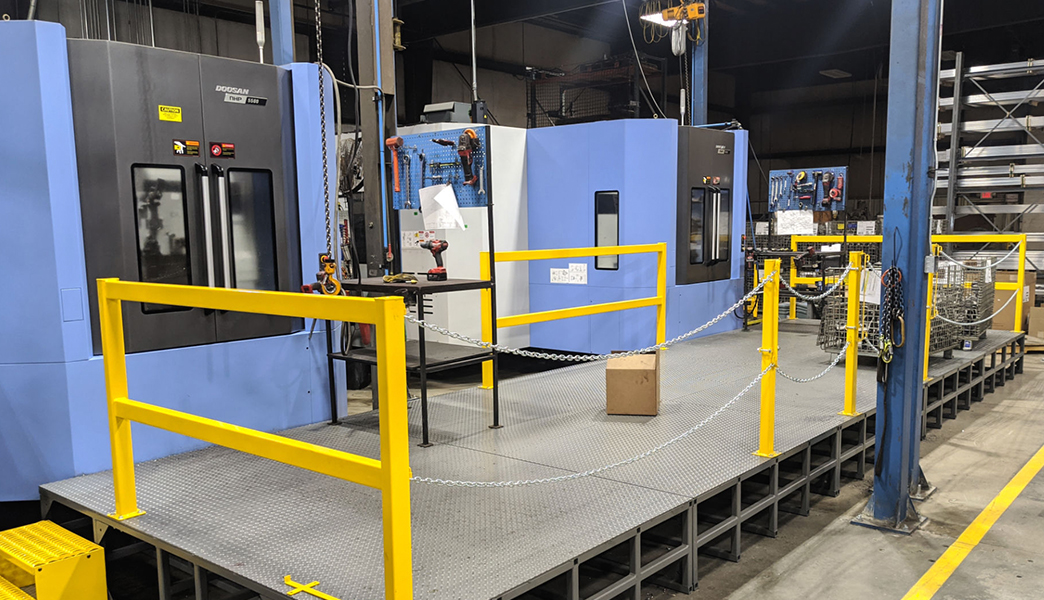
In 2018, Tim presented the benefits of 50 taper horizontal machining in comparison to Link’s current 40 taper machines. Convinced of the improved capabilities 50 taper would provide, Link acquired a Doosan NHP 5500 horizontal machining center (HMC) with 50 hp dual wound spindle motor, 10,000 rpm, 310 ft-lbs. torque spindle, and 19.7” table. Making the switch to the NHP was easy since Link’s previous 40 taper machines had the same table size allowing all their previous fixturing to work on the NHP as well.
Ellison Technologies has been key to offering knowledge of all the different ways of machining with the Doosan product line. "… the cutting capability of the NHP 5500 really caught our attention. It allowed us to use tooling we never dreamed of before and run them harder than ever." – Derek, Link® Manufacturing
Utilizing the rotating pallet and tombstone fixturing, Link was able to setup eight parts per pallet and reduced their cycle time from 60 minutes down to 6 minutes. The advanced workholding created an estimated annual savings of $140,000 a year. The NHP’s B-axis table is capable of holding bi-directional axial tolerance of 0.001” which allowed Link to machine steering knuckle parts that have a wheel hub connecting to suspension and steering components.
"We are also machining bushing surfaces with an 1" end mill with 6" stickout at 190 ipm," Derek said. "The steering knuckles process had a cycle time of 12 minutes that we got down to three minutes after debugging and tuning, allowing us to save about $24,000 per year."
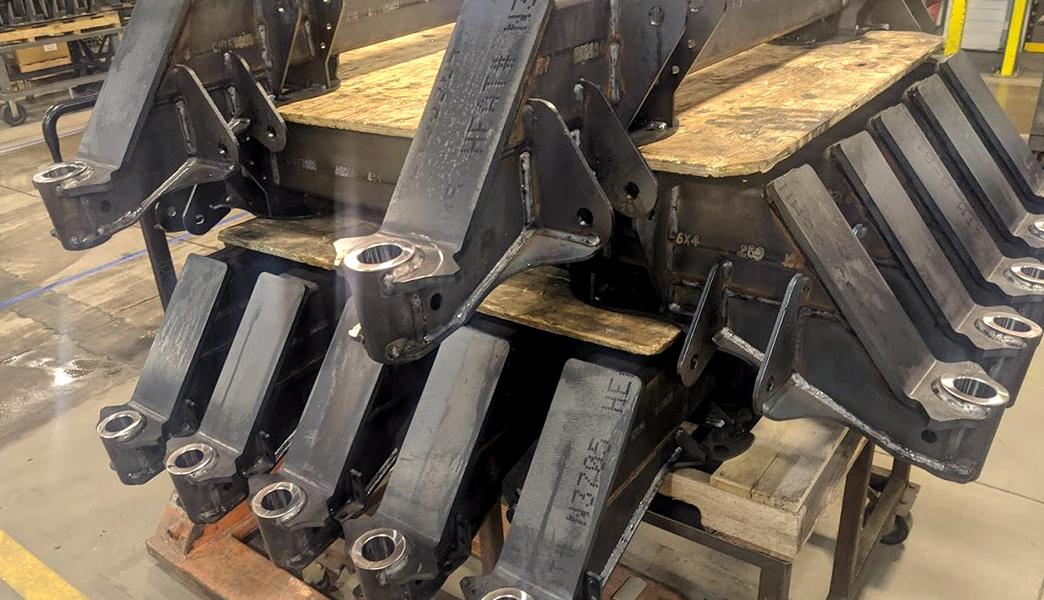
MAKE MORE Money; No More Outsourcing
After experiencing the productive benefits of their first two Doosan machines, Link acquired two horizontal turning centers to bring their originally outsourced round work parts in-house. With the Lynx 2100LSYB and Lynx 2100LB, Link reduced their outsourcing costs and created an additional $284,000 annual savings. Equipped the Lynx with a barfeeder took their productivity even further allow unattended automated machining giving their team the ability to handle more parts at once. In 2019, Link took on second NHP 5500 and discovered additional cost savings from their tooling.
"In this particular application, we were machining a cast part and found 20% extra tool life with the new machine, which equated to $60,000 annual saving in tooling and total cost of production on the part."
Taking advantage of the 90 slot tool magazine, Link has been able to expand their library of parts to be machined on each NHP without having to constantly swap out tools further reducing their setup times.