Machinists are often challenged with coming up with the best finishes possible on intricate parts. This is especially true of those working in the medical and die mold industries. Surgical instruments and bodily implants such as femoral components, bone plates and tibias have to be machined to the most exacting standards.
At Ellison Technologies, our BlueChip Advanced Manufacturing Group helps take your enterprise to the next level. In a nutshell, it takes the vision you have for your business and builds a tailored and realistic plan to get there.
Our BlueChip AMG team has a wealth of experience, and they lent some of it to us for this story.
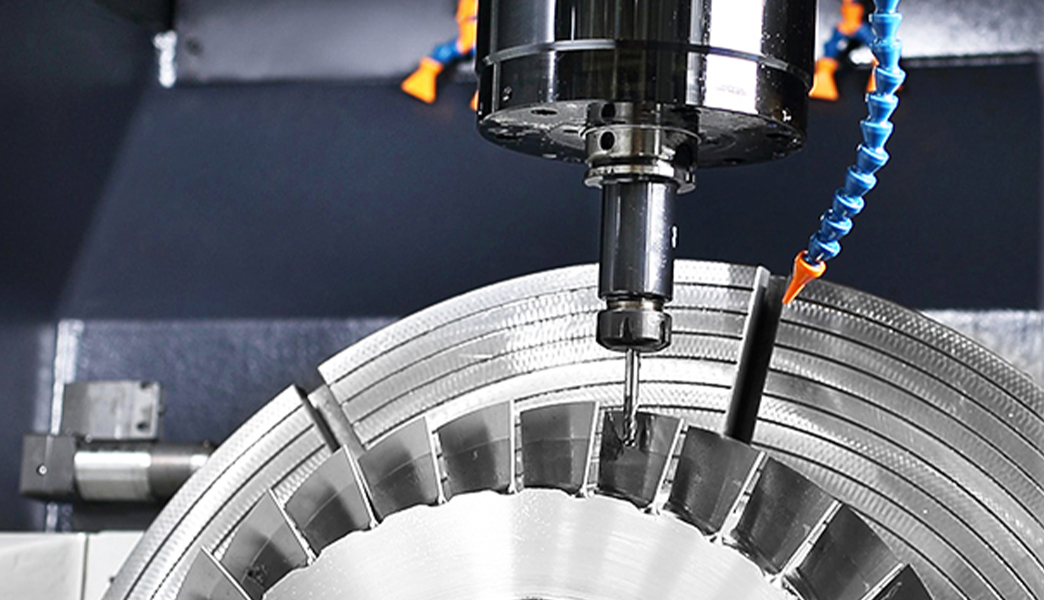

Here’s a Q & A on 5-axis part-making, and how you can achieve the best finishes.
Would you consider machining an art or a science?
It’s actually both. The science side is represented in terms of cutting tool selection, depth of cut and speeds and feeds, etc. But programming functions, such as the style of the toolpath, is an art.
How is the finish quality on a part measured?
Ra (roughness average) is generally the call out that is used. Sometimes Rz (mean roughness depth). It depends on the print. Each manufacturer specifies a range and max. In milling, surface finish better than 32 Ra max is considered good, but you can get down to 14 to 29 Ra depending on the machine tool, technique and part.
Is it possible to achieve that with a multiple setup process?
You can achieve a decent finish with any machine, but at what cost? Multiple setups take time, but to achieve an acceptable finish on a 3-axis machine, for example, you have to slow down the feeds and speeds significantly. That really impacts cycle times.
Why do you have to slow the process down?
Machining a complex part with a non-five axis machine requires using a longer tool in order to reach down into deep, narrow cavities. The longer the tool, the more prone it is to vibration, tool flex and chatter. Slowing feeds and speeds is the only way to mitigate these issues. Otherwise, the result is a less-than-perfect finish. There will also be some difficulties with accuracy when you want to maintain a certain profile.
How does a 5-axis machine eliminate these problems?
A 5-axis machine can rotate the tool holder at a variety of angles, which means you can rotate to a certain lead angle and get the tool and holder closer to the part. The outcome is a much better finish in much less time.

Anything else you like about the DN Solutions (formerly Doosan Machine Tools) DVF machine lineup?
There’s a lot. Thermal compensation features are standard, along with tool load monitoring and adaptive feed rate control. They are also equipped with DSQIII, which is a contour control software to manage the acceleration/deceleration of all the moving axes. A 600 block lookahead and 1GB data server let you stay in the cut longer and remain accurate. And finally, they come with 230 psi high pressure thru coolant, for proper chip evacuation, which is essential for smooth operations.
Are there any options you would recommend for best results with the DN Solutions (formerly Doosan Machine Tools) DVF series?
Not really. They are ready to go right out of the box.
How can programmers contribute to a high-quality finish?
From the programmer’s standpoint, you have to keep the tool at a certain lead angle, so you have to know how to operate the CAM package. For example, taking a ball nose end mill and giving it 10 to 20 degrees to get it off the tip and cut using the radius of the ball. And then finding the optimum cutting speed.
What suggestions can you offer operators?
There are several practical things that an operator should do to achieve the best finish possible. Select tools with the minimum length. Watch for tool run out and check your tools for damage and wear. A collet full of chips or a worn toolholder is really bad for end mills. You won’t get an equal chip load on every flute, which can cause the tool to break.
For fixturing, you want something more rigid, with enough mass to absorb vibrations. Keep it as low to the table as you can get it.
Another thing you have the ability to do with a five-axis machine and the right tool is a swarf toolpath. Take the example of a tapered shark fin shape. Move the rotational axes all at once and keep the cutter constantly engaged to the part. Be sure to engage the full length of the cutter. This results in a smooth finish all the way down the feature of that shape.
Any advice for shop owners and engineers?
Be on the lookout for new technology. Cutting tool companies are coming out with lens form circle segment cutters and conical barrel cutters that have large radius on the side of the cutter. This allows you to program larger step overs or step downs, which leads to quicker cycle times.
Final thoughts?
If anyone has additional questions on 5-axis machining or needs a comprehensive approach to take their enterprise to the next level, they should reach out to the Ellison Technologies team. We’d be happy to help make their vision a reality.